歩留まり改善のための具体的な手法を業界別に解説(自動車業界・半導体業界・エレクトロニクス業界・食品業界)
カテゴリ:基礎知識
ドイツの製造業は、インダストリー4.0によるIoT化やAI 等を使用した第4次産業革命を目指しています。その取り組みは、リアルタイムに製造工場の生産品質データをIoTセンサなどで収集しデータを蓄積します。その後、AI分析を行い、対策を立案して実行する仕組みです。
一方、日本では、ドイツの取組みを参考にした「サイバー空間とフィジカル空間を高度に融合させたシステムの構築」を目指しています。そして、「Society 5.0」と呼ばれる「経済発展と社会的課題の解決を両立する人間中心の社会」の実現に向かっています。
モノ作りの仕組みが変わろうとしている状況で、自社の歩留まりはどのように管理・改善すればよいのでしょうか?
本記事では、歩留まり改善における基本的な考え方とその重要性、及び各業界での管理方法を詳しく解説します。
目次
「歩留まり」の定義と改善の重要性
「歩留まり」は製造業などの業界にとって品質や生産性をあらわす大切な指標です。この指標は生産ラインにおける良品の割合を示しています。高歩留まりは、良い品質や効率的な生産、及び原材料資源の最適な利用を表しています。つまり、歩留まり数値の改善は、品質向上、コスト削減、及び業界内の競争力強化に直結するため、製造業にとっては重要な改善課題となります。
歩留まりの定義とは
歩留まりは、製造業や生産全般において、「原料(素材)の投入量から期待される生産量に対して、実際に得られた製品生産数(量)の比率」を指します。また、歩留まりを百分率で示した数値を「歩留まり率」といいます。
製造業の歩留まりの計算式
製造業界の具体的な計算方法は以下の通りです:
①完成品数に対する原材料数の割合:
②生産数における良品の割合:
食品業界の歩留まり計算式
食品業界の歩留まりは「全体の原材料に対する可食部位の割合」として定義されます。
そのため計算式は以下となります。
①食品生産数における良品の割合:
これらの計算方法は、一般的な方法ですので、取り扱う製品(部品)や業界の特性により異なる場合があります。よって、詳細はそれぞれの業界企業別の基準やガイドラインを参照して下さい。
製造プロセス全体の効率性を測る指標 ・改善の重要性
「歩留まり」は製造プロセス全体の効率性を判断するための重要な指標となります。そして、製造責任者は、製造ラインの歩留まり目標値を定め、関連組織全体が目標に向かうよう働きかけを進める必要があります。
そのためには、以下のような改善活動の継続が重要です。
不良品の発生状況を記録・集計
不良品の種類や発生頻度(不良率)を発生日別、発生時間、発生ロット別などの要素に分けて、4W1H(誰が、いつ、どこで、何を、どのように)が分かるように細かく記録します。また発生頻度が見えるように集計し、グラフなどで傾向が分かるように可視化します。具体的には、午前/午後/深夜、1日、1週、1か月、半年、1年前などの周期で時系列にデータをまとめ、比較できるようにします。
また、不良品の発生工程と不良品の発見工程が異なる場合(後の検査工程で発見された場合)は、発見工程で記録を記載します。
不良の原因分析方法
不良の原因分析法には、一定の型があります。それは、「5M+1E」で不良原因を調査する方法です。以下に5M+1Eについて簡単に説明します。
・材料(Material):
製造で使用する原材料や部品には注意が必要です。購入時の受入検査や、製造時に不良が発見した場合、材料や部品の納入ロットの違いで何か変化は無いか、必ず確認を行います。また必要であれば、材料や部品メーカーに納入ロット別の品質状況を確認することも大切です。
さらに、自社での保管状況(温度・湿度・直射光の影響など)も同時に確認します。
・人(Man):
不良が発生した場合、その発生個所が手作業による工程の場合は、作業員別のデータを取り発生傾向を調べることが大切です。その場合は、作業員のスキルや再トレーニングなどが必要となります。なお、残業や深夜作業なども不良発生の要因となりますので、作業監督者とよく相談し、作業に問題は無いか、作業員自体の体調はどうかなどの確認も必要となります。
・機械設備(Machine)
不良を発生させないためには、生産設備の稼働管理が必要です。例えば、機械設備のアイドリング時や、稼働時に異音/異臭/振動など、常に「いつもと違う事象は無いか?」などの観点で機械設備を監視することが大切です。
また、設備メンテナンスの計画を立て、予防保全により設備のチョコ停、ドカ停を防ぐことが不良の未然防止にも役立ちます。
・方法(Method)
作業手順が正しく行われているかの確認も大切です。作業の進め方は「標準作業指導書(SOP)通りに行われているか」を事細かく確認します。逆に作業手順書自体に「読みにくい/分かり難い/間違えやすい表現は無いか」など、事前に確認し修正すべき点を正すことも重要です。
また、重要な作業の場合は「1人で行うのではなく複数人で実施する」または、「作業の確認は2回行う(Wチェック)」などの工夫も必要です。
・測定(Measurement):
測定設備(計測機付き顕微鏡)や各測定工具の測定精度は、決められた間隔(例:1回/年)で、決められたルールに従い、校正されているか確認することが大切です。これらの測定機器や治工具には、責任者を決めて、校正記録を残し、一定周期で監督者が確認を実施します。
・環境(Environment):
作業環境で大切なことは、モノ作りをする工程の温度・湿度などの環境管理です。特に、ICなどの精密電子部品を搭載する工程では静電気の帯電状況や除電対策が重要になります。また、IC等を製造する工程では、静電気だけでなく塵や埃が少ない環境(クリーンルーム)の管理も必要となります。
それ以外でも、不要なものが製品に混じらないために、5S(整理・整頓・清掃・清潔・躾)や「識別管理の徹底」も重要な管理項目となります。
生産コストの削減と利益率の向上
歩留まりが低下すると、工場の生産性が落ち、利益率が減少します。その原因は、以下のような要因が考えられます。
原材料の不良または過剰仕入れ
不純物の混入がある部品や材料を購入したり、過剰な仕入れによって自社での品質保管期間が過ぎたり、高温・高湿などの保管条件が悪かったりすると、購入した現物は廃棄することになります。そのためこれらの調達にかかったコストを回収できない事態を引き起こします。
機械設備や治工具などの不具合
機械設備による故障や治工具の不具合が発生すると、製品不良が発生し、生産ラインは停止します。それに伴い、製品の歩留まりや生産効率が低下します。
ヒューマンエラー
作業者の不注意や疲労などが原因で作業手順を間違えたりすることがあります。また原材料の投入量や機械の条件設定を誤ったりすることにより、製造歩留まりの低下を招きます。
製品設計段階での見積りミス
設計段階での歩留まりの見積可食部位と、製造段階での実態(歩留まり実績値)が合わない場合があります。結果として実態を計画に合わせようと無理な生産を実施し、不良品を作ることになります。
上述の4つの要因は、歩留まり改善の主因となりますので、課題が発生する前に十分に事前検討することが必要です。
自動車業界における歩留まり改善策
自動車業界の生産方式は、米国フォード・モーター社と日本のトヨタ社が世界的に有名です。米国フォードの特長は、「大量生産」と「標準化」による生産体制です。そのため、一つの製品を大量に生産することにより、製造コストを下げて利益を生み出します。
一方、日本のトヨタ生産方式(TPS)は、「ムダの徹底的排除」をベースにした「ジャストインタイム」と「自動化」です。この生産手法の確立は、企業利益の最大化をもたらします。
この章では、自動車業界における歩留まりの考え方や低下原因、及び改善策について説明します。
自動車業界における歩留まり低下の原因と課題
最近発売される自動車は、リチウム電池を搭載するEV(電気自動車)やHV(ハイブリッド車)の割合が増えつつあります。
また、「CASE」化(Connected ,Autonomous ,Shared& service ,Electric)の進展により、従来のガソリン車に比べ自動車自体の中身が変化しつつあります。その結果、複雑な部品構成による組み立てエラーや、品質管理不足による歩留まり低下が懸念されています。
また、組み立て工場の海外移転や、海外部材メーカー調達により、グローバルレベルのサプライチェーン管理が大きな課題になっています。
上述の課題についての対応策として以下の歩留まり対策が注目を集めています。
自動車業界における歩留まり改善の具体策
上述のような自動車システムの進化により、従来の熟練作業者による車体製造から、AI、IoTセンサ、ロボットなどを使用した製造環境への移行が進んでいます。
自動化とロボット技術
現在、ロボットアームによる自動車組み立てや塗装、自動化された画像検査システムは自動車工場の多くに導入され、生産性の向上が図られています。以下に事例をご紹介します。
自動車組立ラインにおけるロボットアームの導入 事例
1)フランスのPSAグループ(旧社名:PSA・プジョーシトロエン)の自動車工場では、車両のネジ締め作業をロボットアームで行います。
2)欧州フォード社では、導入された協働ロボットが1台当たり約35秒で自動車全体の研磨を実施します。
自動化検査システムの導入事例
1)トヨタ自動車では、自動車のフロントハブ検査工程に、AI画像検査システムを導入し、自動検査を実現しました。これにより検査見逃し率は32%から0%へ改善されました。
品質管理
自動車の品質管理は国際規格IATF16949に従って実施されます。この規格は自動車産業に特有な規格でありIATF(国際自動車産業特別委員会)が制定したものです。
対象となる企業は、自動車の製造段階で使用される製品や部品のメーカーであり、第三者審査機関がサプライヤー審査と登録を実施します。なお、2016年に「IATF16949(初版)」が発行されています。
設備監視
トヨタ自動車(北海道)では、新型自動車(Y)の生産ラインについてIoTシステムを導入しました。具体的には搭載する駆動ユニットの生産工程にIoTセンサを導入し、稼働状況を可視化した結果、生産性は3倍まで向上しました。
半導体業界における歩留まり改善策
半導体業界の製造歩留まりは、一般に「シリコンウェハー」上に形成する半導体素子(チップ)の良品の割合を示しています。半導体製造プロセスは、非常に微細なパターン形成が求められる工程です。そのため、塵埃を極端に少なくする高度な工程管理が求められています。
歩留まり改善は、製品の品質向上だけでなく原材料の使用量を減らし、生産性を改善し、製品コスト削減など、さまざまなメリットをもたらします。
例えば、ウェハーの大きさにもよりますが1枚当たりのウェハー上の半導体素子(チップ)は、数百~数千個になります。そのため、歩留まり改善効果は、良品数の増加に大きく寄与します。
半導体業界における歩留まり低下の原因と課題
半導体製造における歩留まりの重要な要素は、①「フォトリソグラフィ工程の不良」、②「化学薬品の品質変動」、③「クリーンルームの微細な汚染 」です。
フォトリソ工程は、微細な回路パターンをウェハー上に形成する工程です。現在、回路パターンの配線幅がナノオーダーで微細化が進むなか、EUV露光技術や使用される感光材料フォトレジスト、エッチング液などの品質低下が歩留まりに影響を及ぼしています。
また、半導体素子を形成する工程のクリーン度(クリーンルームの清浄度)も歩留まりを変動させる大きな要因です。つまり、クリーン度の低下による微細なダストの発生は、ウェハー上の素子に欠陥を引き起こす結果となります。
半導体業界における歩留まり改善の具体策
半導体製造の重要工程は、ウェハー上に半導体素子を形成する「露光~現像~エッチング工程」(フォトリソグラフィ―)です。この工程での品質をいかに高めるかが歩留まりを高く維持するためのポイントです。そのために、各プロセスの精密制御や環境管理が重要となります。
精密制御
半導体製造の露光現像工程は、回路パターンや配線パターンを形成する工程です。回路配線用フォトマスクに異物や埃などの粒子付着は、回路や配線パターンの欠陥を引き起こす可能性が非常に高くなります。そのため、異物粒子の組成を分析して発生原因を特定し、異物粒子の発生を抑えることが必要です。これにより工程の品質を向上させることが可能になります。
また、エッチング工程は、露光現像後に不要な部分を物理的、または化学的に除去する工程です。微細パターンを削り取るスピード(エッチングレート)の精度は、半導体の品質に大きく関係します。特に、回路の細かな部分が正確に取り切れない場合は半導体の電流の流れなどを阻害することになります。そのため、エッチングレートの制御は非常に重要となります。
環境管理
半導体製造で使用されるクリーンルームは、歩留まりを維持するうえで重要です。上述の露光現像工程やエッチング工程では、微細な異物(塵埃など)の侵入を防ぐことが大切です。その為、クリーンウエアの装着、クリーンルームの清掃はもちろんですが、空気の流れに潜む異物を除去するためのHEPAフィルターの選定や定期的な交換が必要です。
また、クリーン度のモニタリングを定期的に実施し、クリーン度(例:クラス10、クラス100など)が一定の数値内に維持管理されていることを確認しなければなりません。
化学薬品を使用する工程(ドライエッチング、ウエットエッチングなど)では、使用する薬品の純度や薬液中の微量金属を管理することが重要です。特に、薬液中に存在する微量金属(不純物)は、半導体の電気特性や加工形状に影響を及ぼすため、分析装置(ICP-MSなど)で判別することが必要となります。
データ解析
半導体製造工程における不良(欠陥)の発生原因は非常にさまざまな要因から成り立っています。そのため、AIやビックデータを使用して出来るだけ早くその要因を突き止めて、対策を実施することが歩留まりや生産性向上に大きく寄与します。
例えば、各種センサーデータから異常値を発見する事や、生産品質上のデータから異常な傾向を特定するなど、その利用価値は非常に高いものとなります。
エレクトロニクス業界における歩留まり改善策
エレクトロニクス業界における歩留まり改善には、いくつかの方法があります。歩留まりは、製品の収益性や生産の効率性を把握するために重要な指標であり、投入した原材料によって生産された製品に対して良品が占める割合を指しています。
現在、パソコン、家電製品、スマートフォンなどのエレクトロニクス製品は小型化や高機能化が進んでいます。それに伴い、使用される部品は従来に比べて複雑になり、より精度の高い生産ラインの管理が求められています。そのため、歩留まりの改善には、より質の高い手段が要求されています。
エレクトロニクス業界における歩留まり低下の原因と課題
エレクトロニクス業界における歩留まり低下は、主に①製造プロセス、②設備管理、③材料品質、④作業手順など多くの要因によって引き起こされます。特に重要な共通課題である、「プリント基板工程の歩留まり」を例に取り、以下に課題の対策を説明します。
PCB(プリント基板)製造における回路の微細な断線
多層のPCB基板は複雑な内部構造を持ち、精密電子部品を基板上に配置するための部品です。PCB上やPCB内の微細な断線は、電気回路の接続が不完全になることを意味します。そしてこれは歩留まり低下の主な原因の一つになります。
はんだ付け工程での不良
はんだ付けは電子部品を基板に接続する重要な工程です。不良はんだ付けにより、電気回路の信頼性が低下したり、精密電子部品を破壊したりして歩留まりが悪化します。そのため、鉛フリーの半田材料の選定や、半田層の温度管理(温度プロファイル)や、仕上がり形状の管理など、多くのポイントを適切に管理することが重要です。
エレクトロニクス業界における歩留まり改善の具体策
エレクトロニクス業界におけるプリント基板工程の歩留まりは、精密電子部品の搭載精度やはんだ付けの品質に左右されます。この工程では、精密電子部品を遅滞なく正確に定められた場所に挿入し、その後、適切な半田で正しく溶着できることが重要ポイントとなります。
一般にはんだ付け工程は、認定されたはんだ付け作業員の手作業、及び自動されたSMT(表面実装装置:Surface Mount Technologyの略)で実施されます。そのため、はんだ付け作業の管理やSMT管理の良し悪しが、製品の歩留まりに直結します。
製造プロセスの自動化
製造プロセスで使用するはんだ付けロボットは、産業用ロボットの一つで、主にはんだ付け作業を行います。その作業品質は、熟練作業者に代わるほどの高度な作業を再現できます。
初期のはんだ付けロボットは、「半田ごて」の先端に「はんだ」を付けるだけの作業でした。しかし「鉛フリーはんだ」への移行に伴い、ロボットを採用する企業の割合は増加しています。以下にはんだ付け工程の歩留まり改善に欠かせない「自動はんだロボット装置」と「AOI検査装置」の概要について説明します。
自動はんだ付けロボットの導入
自動はんだ付けロボットは、細かな箇所への精密な部品搭載や、耐熱性が弱い電子部品の搭載、及びはんだ付けが得意です。このロボットは、熟練作業者に比べて高い精度ではんだ付け作業を長時間連続(24時間以上)で実施することが可能です。このため、熟練作業者の技術継承や、作業員不足に対応する代替手段として注目されています。
AOI(自動光学検査)の利用
自動光学検査(Automated Optical Inspection;AOI)は、プリント基板を検査する自動検査装置です。AOIは人間の目視検査に代わり導入された実装基板検査装置であり、自動検査が可能です。
AOIは高解像カメラにより基板表面(裏側・表側の両方)に搭載された電子部品やはんだ付け部分の状態を撮影し、基板上の品質を確認します。具体的には、以下の異常を瞬時に判定します。
①電子部品の欠損やずれ・傾き・実装漏れ、
②部品の端子部のはんだ過不足
③部品の誤実装、位置や向きの間違い
④配線部のショート・オープン
品質管理と検査
ICT(インサーキットテスト)の導入
ICTは、プリント基板に電子部品が搭載された後、実装された基板が所定の性能を発揮するか否かを、電圧や電流を測定して確認する装置です。
この検査により、以下のような項目を確認します。(以下は代表的な内容です)
①電子部品の種類やグレード
②回路基板上の配線の断線有無
③はんだ不良
④ダイオードの極性
⑤ICやトランジスターの動作
X線検査装置の使用
X線検査は電子部品がプリント基板に実装された状態を確認する方法です。電子部品と基板の接続部は、非常に狭くなっており通常の目視では確認できません。そのため部品や基板を透過するX線を使用して、ボールグリッドアレイ(BGA)などの接続状態やはんだ部の状態を確認します。この検査によりはんだブリッジ、クラック、ボイドなどの欠陥を発見することができます。
工程改善
DFMA(設計と製造の一体化)手法の導入/
DFMAは(Design for Manufacture and Assembly の略)で、製造と組み立ての設計と呼ばれています。この設計手法は、①製品の作り易さと②部品の組み立てし易さを同時に達成する方法です。
①製品の作り易さ:
設計段階で、製造作業の複雑さを最低限に抑える手法です。なお費用対効果も同時に検討します。
②使用する部品を完成品に組み立てる容易さ:
個々の部品点数、組み立て手順、組み立て品質のバラツキを抑える設計を目指す手法です。
5S活動の徹底
5Sとは、整理・整頓・清掃・清潔・躾の5つの頭文字をまとめた言葉です。その目的は、製造現場を含む職場環境の全てをあるべき姿に整備することです。そのため、5Sを実施することにより作業環境の効率を高め、歩留まりを含めた高品質を長い間にわたって維持することが可能になります。
例えば、作業現場が整理・整頓されていれば、必要な工具や部品を探す手間が無くなります。また、つねに清掃を行い清潔な状態を保てば、機械設備の故障も少なくなります。さらに、きれいな作業環境を保てば、作業者の安全確保にもつながります。
食品業界における歩留まり改善策
食品業界における歩留まり改善は、工場の生産効率を上げ、利益を最大化するための重要なテーマです。食品の歩留まりを改善するには、原材料の適切な管理、製造プロセスの最適化、廃棄物削減がキーポイントとなります。そのため、単なる工程改善によるコスト削減策だけでなく、製造工程の改善をAIやIoTなどの新技術を導入し歩留まり向上を図ることが大切です。
食品業界における歩留まり低下の原因と課題
食品業界における歩留まり低下の原因と課題について、以下の3つの観点からまとめます。
1.原材料の品質不均一
購入した原材料の品質が不均一であると、出来上がった製品の品質や味が一定になりません。このような食品が出荷されると顧客満足度が下がり、ブランドイメージを損なうことになります。また、品質の低い原材料では食品加工中に不具合品(食品ロス)が発生する懸念があり、歩留まりが低下します。
2.加工工程での食品損失や食品ロス
加工工程における食品損失(製造工程で発生する廃棄物など)や食品ロス(食べられるが期限が切れて廃棄されるものなど)は、生産効率を大幅に低下させる可能性があります。発生原因は、機械の故障、操作ミス、または生産スケジュールの遅れなどにより引き起こされる課題です。これらの問題は、生産コストの増加と歩留まりの低下につながります。
3.パッケージング不良
パッケージング不良は、食品の味・臭い・見た目などの品質や鮮度に大きく影響します。そして、この不良は食品の廃棄につながります。
食品業界における歩留まり改善の具体策
食品業界における歩留まり改善の具体策は、生産効率と利益を最大化するための重要な戦略です。この取り組みは、コスト削減だけでなく、持続可能性の向上にもつながります。食品業界がこれらの改善策を採用することで、より効率的で持続可能な未来を実現することができます。以下に3つの観点から改善策を説明します。
原材料の管理
原材料の品質管理
食品業界における歩留まり改善の一つの重要な観点は、原材料の品質管理です。原材料の品質が一定でないと、製品の品質や味が一定しない可能性があり、これが損失を引き起こします。特に、供給元の選定、原材料の受入検査、原材料の保存方法が重要です。
先入れ先出し(FIFO)方式の徹底
食品の先入れ先出し(FIFO)方式とは、最初に入荷した商品を最初に出荷するという在庫管理の方法です。これにより、商品の鮮度を保つことができ、食品の品質低下や廃棄を防ぐことができます。
製造工程の最適化
高精度な切断機器の導入
食品加工に高精度な切断機器を導入することは、原材料の切断精度を向上させ、食品サイズを一定に保つことができます。この結果、加工された食品サイズの大きさバラツキが抑えられ、顧客満足度が向上します。
また、高精度な切断機器は、原材料の無駄を減らし、製品の歩留まりを向上させます。具体的には、切断精度の向上により、原材料の余分な部分を削減し、必要な部分だけを使用することが可能となります。
自動計量システムの使用
食品加工に自動計量システムを使用することで、原材料の使用量を正確に制御し、製品の重量を一定に保つことができます。これにより、製品品質が安定し、顧客満足度が向上します。
品質管理
HACCP(ハサップ)システムの導入
食品業界における歩留まり改善策として、「HACCP(ハサップ)システムの導入」があります。HACCPは、食品の安全性を確保するための国際的な基準です。そのため、食品製造工程で各段階での危険要因を特定し、それらを管理することを目的としています。
リアルタイムモニタリングシステムの導入
リアルタイムモニタリングシステムは、食品加工ラインの稼働状況をリアルタイムで監視します。その結果、加工データを収集し分析する機能を有しています。もし、製造ラインに問題が発生した場合は即座に対処することが可能となり、食品品質を維持しながら、歩留まりを向上させることができます。
まとめ
製造業における具体的な歩留まり改善手法は業界別に異なります。自動車、半導体、エレクトロニクス、食品の各業界では、歩留まり低下の原因と課題は異なるため、共通する手法(5M+1E)を活用しつつ、問題を分析し、改善策に繋げることが大切です。主な改善策として、製造プロセスの自動化、品質管理の強化、データ解析の活用、環境管理の徹底などが挙げられます。また、AIやIoTなどの新技術導入による歩留まり向上が今後の重要なポイントとなります。
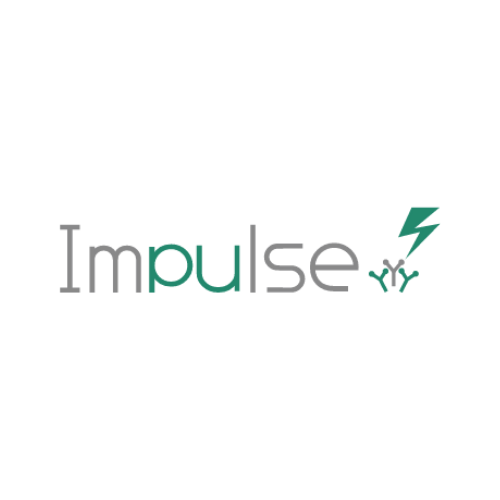
- Impulseによる製造業における歩留まり改善
- Impulseは製造業における歩留まり改善を強力に支援する異常検知ソリューションです。2014年に市場に先駆けてリリースされ、多くの製造現場で実績を積み重ねてきました。製造プロセスから生成される複雑で膨大なセンサデータ、音声、画像、動画などを収集・可視化する基本機能に加え、機械学習技術を駆使して従来の閾値管理では発見できなかった微細な異常や不良品を高精度に検出します。
さらに、不良発生の予兆を早期に捉え、要因分析を支援することで、歩留まり低下を未然に防ぎます。Impulseは、これまで対応が困難だった歩留まり改善の課題に対し、新たなアプローチで具体的な解決策を提供し、製造ラインの生産性と品質向上に貢献します。