サイクルタイムの短縮方法。金属加工と樹脂成形におけるボトルネックの特定と改善
カテゴリ:基礎知識
製造業において、サイクルタイムの短縮は生産性向上とコスト削減の鍵を握っています。
しかし、複雑な工程やボトルネックの存在により、改善は容易ではありません。
本記事では、金属加工と樹脂成形を例に、それぞれの工程を分解し、サイクルタイム短縮のための具体的な方法を紹介します。
サイクルタイムとは?
「サイクルタイム」(Cycle Time)とは、特定のプロセスや作業が開始されてから完了するまでにかかる時間を指します。
製造現場におけるサイクルタイムは、生産性向上を図る上で欠かせない指標です。サイクルタイムが短縮できれば、それだけ多くの製品を製造できるようになり、コスト削減や納期短縮などに繋がります。
サイクルタイムは、以下の式で求められます。
この章では、サイクルタイムの基本的な定義から、類似する指標であるタクトタイムやリードタイムとの違いまで、分かりやすく解説していきます。
タクトタイムとの違い
サイクルタイムと混同しやすい指標に「タクトタイム」(Takt Time)があります。両者は似ていますが、定義は異なります。生産計画を立てる上では、それぞれの違いを正しく理解することが必要です。
タクトタイムとは、1つの製品を製造するのに必要な時間のことで、以下の式で求めることができます。
例えば、1時間に20個の製品を製造する必要がある場合、タクトタイムは3分になります(60分÷20個 =3分/個)。つまり、3 分ごとに1個の製品を完成させないと、顧客の需要に追いつけません。
サイクルタイムは「1つの製品を生産するのに必要な時間」であるのに対し、タクトタイムは「顧客の需要を満たすための製品1つあたりの生産時間の目標値」です。サイクルタイムは実際の生産速度を表し、タクトタイムは顧客の需要にもとづく理想的な生産速度を示す指標です。
製造現場では、サイクルタイムをタクトタイム以下に抑えることで、計画通りの生産が可能になります。
リードタイムとの違い
サイクルタイムと混同しやすい指標に、「リードタイム」(Lead Time)があります。リードタイムは顧客が製品を注文してから、実際にそれを受け取るまでにかかる時間を指します。
例えば、顧客がオンラインストアで商品を注文してから、自宅に届くまでにかかる時間がリードタイムです。
リードタイムには、製造に必要な時間だけでなく、受注処理、在庫管理、配送などの時間も含まれます。そのため、リードタイムはサプライチェーン全体の効率性を測る指標として用いられます。
サイクルタイムを短縮すれば、リードタイムも短縮される可能性があります。しかし、リードタイムは製造以外の要素にも影響を受けるため、サイクルタイムの短縮が必ずしもリードタイムの短縮に直結するわけではありません。
︎サイクルタイム・リードタイムなど、製造現場における時間指標の違いについて、詳しくは以下の記事をご覧ください。
関連記事:タクトタイム・サイクルタイム・リードタイムの意味や違い&改善方法
金属加工におけるサイクルタイムの短縮
金属加工は、素材の切断から複雑な形状の加工まで、多くの工程を経て製品が完成します。各工程にかかる時間は、製品の品質はもちろん、生産効率に直結する重要な要素です。
特に、大量生産が求められる製造現場においては、1つひとつの工程のサイクルタイム短縮が、生産能力の向上、コスト削減、そして納期短縮を実現する鍵となります。
この章では、金属加工における代表的な工程を具体的に分解し、それぞれの工程におけるサイクルタイム短縮のための方法を紹介します。
金属加工における作業工程を分解する
金属加工は、素材を切断し、工作機械を用いて目的の形状に加工していく工程です。ここでは、CNC加工機による金属加工の工程を具体的に分解し、各工程の概要とサイクルタイムへの影響について解説します。
1. 素材の切断
工程の概要
金属板やパイプなど、製品の原材料となる素材を必要な大きさに切断します。切断方法には、シャーリング加工、レーザー加工、ウォータージェット加工など、素材や形状、寸法精度によって最適な方法が選択されます。
サイクルタイムへの影響
素材の大きさや材質、切断方法によって大きく時間が変動します。高精度な切断や複雑な形状の加工には時間がかかるため、サイクルタイム短縮のためには、適切な切断方法の選定や加工機の性能が重要となります。
2. 工作機械の設定
工程の概要
工作機械の設定を行います。CNC加工機は、CADデータや図面を基に作成されたプログラムによって動作します。この工程で、製品の形状や寸法、加工条件などが定義されます。
サイクルタイムへの影響
複雑な形状の加工や高精度な加工は、プログラムが難しくなるため、設定に時間がかかる場合があります。サイクルタイム短縮には、CAMソフトウェアの活用による自動化が有効です。
3. 工具・材料の設置
工程の概要
加工に必要な工具と、前工程で加工した素材を準備し、CNC工作機械に取り付けます。
素材の大きさや形状によっては、クランプや治具を用いて固定しなければなりません。
サイクルタイムへの影響
素材の大きさや形状、重量によって設置時間が変動します。また、設置精度が加工精度に影響するため、慎重な作業が必要です。サイクルタイム短縮には、作業性の良い治具の導入や、ロボットによる自動化などが考えられます。
4. 材料の加工
工程の概要
CNC工作機械を用いて、素材の切削、穴あけ、溝入れなどを行い、目的の形状に加工します。工具の選定や切削条件の設定によって、加工精度や表面粗さが大きく変化します。
サイクルタイムへの影響
加工する形状の複雑さや寸法精度、材質によって加工時間が大きく変動します。サイクルタイム短縮には、適切な工具の選定や切削条件の設定、高剛性な工作機械の導入などが重要となります。
5. 完成品の取り外し
工程の概要
加工が完了した製品をCNC工作機械から取り外します。クランプや治具を使用している場合は、それらも取り外す必要があります。
サイクルタイムへの影響
材料の設置と同様に、素材の大きさや形状、重量によって取り外し時間が変動します。サイクルタイム短縮には、作業性の良い治具の導入や、ロボットによる自動化などが考えられます。
6. 仕上げ加工
工程の概要
必要に応じて、バリ取り、研磨、表面処理などを行い、製品の表面を仕上げます。
サイクルタイムへの影響
仕上げ加工の方法は、製品の用途や要求される品質によって異なります。サイクルタイム短縮には、工程の統合や自動化、効率的な工具の採用などが有効です。
7. 検査
工程の概要
完成した製品が図面通りに加工されているか、外観に問題がないかなどを検査します。ノギスやマイクロメーターなどの測定器を用いた寸法検査や、目視による外観検査が行われます。
サイクルタイムへの影響
検査項目や検査方法によって検査時間が変動します。サイクルタイム短縮には、検査工程の自動化や、品質管理システムの導入による検査データの効率的な管理などが考えられます。
上記のように各工程を分解し、所要時間の計測・分析を行えば、ボトルネックとなっている工程を特定することができます。ボトルネック工程を改善すれば、サイクルタイムの短縮につながるでしょう。
時間短縮可能な工程の特定
金属加工では、一体どの工程に時間短縮の余地があるのでしょうか。前述の工程を踏まえて見ていきましょう。
ボトルネックの特定
サイクルタイム短縮には、まず現状におけるボトルネックを正確に把握することが必要です。ボトルネックとは、工程全体の中で最も時間のかかる工程や工程間の滞留を指し、ここを改善することでサイクルタイム短縮の効果が最大化されます。
現状分析の第一歩は、各工程の所要時間を計測し、可視化することです。前述のように工程を分解し、作業時間や待ち時間などの実測値を記録します。
例えば、金属加工の工程において
- 素材の切断:1個あたり5分
- CNCの設定:1個あたり10分
- 工具・材料の設置:1個あたり5分
- 材料の加工:1個あたり8分
- 完成品の取り外し:1個あたり2分
- 仕上げ加工:1個あたり3分
- 検査:1個あたり4分
という計測データが得られたとします。この場合、CNCの設定に最も時間がかかっていることが分かります。
ボトルネックとして特定された工程については、工程内の各作業要素にどれだけの時間がかかっているかを分析する必要があります。
次に、各作業要素における動作を分析し、無駄な動きや非効率な手順がないかを洗い出しましょう。それに加え、設備の稼働状況や性能を分析し、ボトルネック発生の原因が設備側にないかを検証します。
これらの分析を通して、ボトルネック工程における具体的な改善ポイントを明確化します。
改善ポイントの明確化
サイクルタイム短縮のための改善ポイントは、大きく2つに分けられます。
自動化の導入が可能な工程
ロボットや専用機を導入することで大幅な時間短縮を実現できます。
手動作業の効率化が求められる工程
自動化が難しい工程や、現時点では自動化がコストに見合わない工程については、手動作業の効率化によってサイクルタイムを短縮する必要があります。
手動作業の効率化に関しては、比較的低コストで実施できるものが多く、大きな効果が期待できます。現場作業者からの意見を積極的に聞き取り、改善活動を進めることが重要です。
時間の短縮
これまで解説してきた工程分析やボトルネックの特定方法に基づいて、具体的なサイクルタイム短縮手法を導入すれば、生産性の向上を実現できるでしょう。
本章では、金属加工における時間短縮に効果的な方法を紹介します。
自動化の導入
製造現場におけるサイクルタイム短縮には、自動化の導入が不可欠です。特に、これまで人手に頼っていた工程を自動化すれば、大幅な時間短縮と生産性の向上が見込めます。
自動化の導入効果を最大限に引き出すためには、以下のポイントを押さえることが重要です。
費用対効果の検証
初期費用だけでなく、ランニングコストやメンテナンス費用も考慮し、投資に見合う効果が得られるかを慎重に検討しましょう。
工程全体の最適化
自動化する工程だけでなく、前後の工程も含めた工程全体を最適化することで、より大きな効果が期待できます。ボトルネックとなっている工程を重点的に自動化し、工程全体の効率化を目指しましょう。
段階的な導入
最初から全ての工程を自動化するのではなく、効果が見込める工程から段階的に導入していくことで、リスクを抑えながら自動化を進めることができます。
従業員の教育・訓練
自動化によって新たに生まれる業務や、自動化設備の操作・保守に必要な知識・技能を習得するための教育・訓練を従業員に提供することで、円滑な自動化設備導入を実現できます。
上記のポイントを踏まえたうえで、自動化に取り組みましょう。
具体的には、以下のような事例が挙げられます。
- 材料の搬送や材料の取り外しをロボットアームで行う。
- 自動工具交換装置が搭載されているCNC加工機を導入し、工具の交換時間を短縮する。
機械学習を活用した分析サービスを利用する。 - 自動化は、サイクルタイム短縮だけでなく、人材不足の解消、品質の安定化、労働環境の改善など、様々なメリットをもたらします。
上記を参考に、自社の課題や状況に合わせて適切な自動化を行うことで、生産性向上や競争力強化を実現できるでしょう。
プロセスの改善
製造現場におけるサイクルタイム短縮は、自動化導入だけがすべてではありません。既存の作業手順や設備、作業者に対するアプローチを見直すことでも、大幅な改善が見込めます。
そこで、以下の流れで現状における作業手順を詳細に分析し、無駄な動作や工程、待ち時間などを洗い出してみましょう。
- 現状分析
現在の作業手順を、体系表やフローチャートなどを用いて可視化します。 - 無駄の排除
工程や動作の順番、移動距離、作業姿勢、使用工具などを精査し、無駄な要素を排除します。 - 標準化と文書化
改善後の作業手順を標準作業手順書としてまとめ、作業者全員が共有できるようにします。写真やイラストを積極的に活用し、理解しやすい手順書を作成しましょう。 - 教育・訓練
作成した標準作業手順書に基づき、作業者への教育・訓練を実施します。手順の変更点や重要ポイントを重点的に指導することで、標準手順の定着を図ります。 - 継続的な改善
定期的な見直しを行い、作業環境や設備の変化に合わせて、手順を継続的に改善していくことが重要です。
上記のポイントを踏まえたうえで、プロセスを改善しましょう。
具体的には、以下のような事例が挙げられます。
- 動作分析やムダ取りの手法を用いて、作業動作を分析し、無駄な動きや非効率な手順を排除する。
- 作業スペースの整理整頓、必要な工具の配置場所の見直し、適切な照明の設置など、作業環境を改善することで、作業効率を向上させる。
- 標準作業手順書を作成し、作業者への教育を徹底することで、作業のバラつきを抑え、品質の安定化とサイクルタイムの短縮を図る。
- 作業補助用の治具を導入することで、作業の効率化と品質の安定化を図る。
どんな作業にも、効率的な手順と非効率な手順が存在します。長年現場で行われてきた作業の中には、非効率な手順が当たり前になってしまっているケースも少なくありません。まずは現状における作業手順を詳細に分析し、無駄な動作や工程、待ち時間などを洗い出してみましょう。
設備のアップグレード
老朽化した設備を使い続けることは、パフォーマンスの低下や故障のリスクを高め、結果的にサイクルタイムの増加につながります。最新の設備は、処理速度の向上、自動化機能の搭載、省人化、品質の安定化など、サイクルタイム短縮に大きく貢献します。
ただし、設備導入は高額な投資となるため、導入費用と期待される効果を比較検討し、投資対効果を慎重に見極めることが重要です。
樹脂成形におけるサイクルタイムの短縮
金属加工と同様に、樹脂成形においてもサイクルタイムの短縮は、生産性向上、コスト削減、そして納期短縮を実現する上で非常に重要です。特に、大量生産が求められる現場では、1秒の短縮が大きな成果に繋がることもあります。
この章では、樹脂成形における代表的な工程を具体的に分解し、それぞれの工程におけるサイクルタイム短縮のための方法を紹介します。
樹脂成形における作業工程を分解する
樹脂成形は、プラスチック材料を溶融状態から金型へと流し込み、冷却・固化させることで製品を製造する技術です。製品形状や用途、生産量に応じて、様々な成形方法が用いられます。
この章では、樹脂成形における代表的な作業工程を具体的に分解し、それぞれの工程の概要とサイクルタイムへの影響について解説します。
1. 材料の準備工程
工程の概要
原材料である樹脂ペレットを乾燥させ、着色剤や添加剤を配合します。
サイクルタイムへの影響
ペレットの乾燥時間の調整、配合精度、材料の搬送距離や搬送方法を適切に管理することでサイクルタイムを短縮できます。
2. 成形工程
工程の概要
溶融した樹脂を金型に注入し、冷却・固化させて成形を行います。射出成形、ブロー成形、押出成形など、様々な成形方法があります。
サイクルタイムへの影響
金型の開閉速度の短縮、射出速度や樹脂温度、保圧時間の適切な管理がサイクルタイム短縮につながります。
3. 冷却工程
工程の概要
金型内で成形された製品を十分に冷却し、変形を防ぎます。
サイクルタイムへの影響
一般的に、冷却工程が占める時間の割合が最も多い工程です。冷却時間を短縮すれば、サイクルタイムの短縮にもつながります。
4.取り出し工程
工程の概要
冷却が完了した製品を金型から取り出します。
サイクルタイムへの影響
成形工程同様、金型の開閉速度の適切な管理がサイクルタイム短縮につながります。
5. 仕上げ加工工程
工程の概要
ゲートカット、バリ取り、穴あけなどを行い、製品を仕上げます。
サイクルタイムへの影響
作業効率や工具の性能によってサイクルタイムが変動します。
6. 検査工程
工程の概要
製品が図面通りに成形されているか、外観に問題がないかなどを検査します。
サイクルタイムへの影響
検査項目や検査方法によってサイクルタイムが変動します。
時間短縮可能な工程の特定
樹脂成形において、サイクルタイムに大きな影響を与える工程を特定することが、生産性向上への第一歩です。この章では、樹脂成形の工程を具体的に分析し、時間短縮の鍵となる工程を紹介します。
ボトルネックの特定
金属加工と同様、各工程にかかる時間を計測し、可視化することが必要です。各工程にかかる実測値を確認しましょう。
ボトルネック工程内の各作業要素にどれだけの時間がかかっているかの分析、無駄な手順の洗い出しを行う必要があります。
改善ポイントの明確化
前述の通り、サイクルタイム短縮を実現するにはボトルネックを特定し、適切な改善策を講じることが必要です。
特に効果の高い改善ポイントとして、「冷却時間の短縮」と「自動検査装置の導入による検査工程の効率化」が挙げられます。
樹脂成形において、冷却時間はサイクルタイムの大部分を占めることが多く、この時間を短縮することで大幅な効率化が期待できます。
自動検査装置は、カメラを用いた外観検査、センサーを用いた寸法検査など、様々な種類があります。検査対象や要求される精度、予算に合わせて最適な装置を選択することが重要です。
時間の短縮
樹脂成形において、成形サイクルは生産性に直結する重要な要素です。このサイクルを1秒でも短縮することが、生産量増加、コスト削減、そして納期短縮といった大きな成果に繋がります。
本章では、成形サイクルを構成する各要素を細かく見直し、最適化を図るための具体的な方法を紹介します。
成形サイクルの最適化
例えば、射出成形機の設定は、成形サイクル、そして製品品質に大きな影響を与えます。これまで、射出成形機の設定は、担当者の経験に頼っていました。
しかし、経験や勘だけに頼るのではなく、データに基づいた科学的なアプローチを取り入れることで、より効率的かつ安定した生産体制を構築できます。
冷却プロセスの改善
サイクルタイムの大部分を占める冷却工程の時間を短縮することが、生産性向上のための重要な鍵となります。冷却時間を短縮するためには、高効率な冷却装置の導入や、冷却時間の短縮技術の導入が有効です。
例えば金型温度調節機、ミスト冷却など、より短時間で効率的に冷却を行うことができる高効率な冷却装置が数多く開発されています。
冷却時間の短縮には、高効率な冷却装置の導入だけでなく、冷却効率を考慮した金型設計や樹脂材料の見直し、成形条件の見直しなども有効です。
自動化導入
自動化は、人手に頼っていた作業を機械化することで、サイクルタイムの短縮、人材不足の解消、品質の安定化、労働環境の改善などの効果が期待できます。具体的には自動搬送システムやロボットアームの導入などです。
金属加工と同様、自動化の導入効果を最大限に引き出すためのポイントを考慮して取り組みましょう。
まとめ
本記事では、製造業における永遠のテーマであるサイクルタイム短縮について、金属加工と樹脂成形を例に、具体的な方法を工程ごとに詳しく解説しました。サイクルタイム短縮は、以下の3つのポイントを軸に改善を進めることが重要です。
1. ボトルネックの特定と工程の可視化
2. 工程の自動化
3. 設備のアップグレードとプロセスの効率化
サイクルタイムの短縮は、「一度対策すれば終わり」ではありません。生産計画や外部環境の変化に応じて、継続的に工程を見直し、改善を続けることが、生産性向上へとつながります。
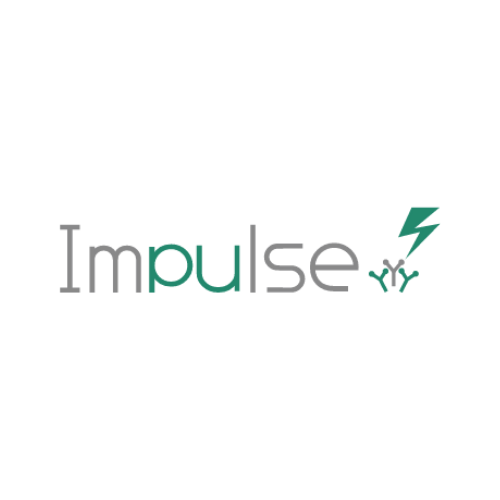
- Impulseによるサイクルタイム短縮
- 製造現場におけるサイクルタイム短縮は、生産性向上、コスト削減、納期短縮といった企業競争力を強化する上で非常に重要です。本記事で紹介したように、ボトルネックの特定、工程の自動化、設備のアップグレードなど、様々なアプローチがありますが、これらの取り組みをより効果的に推進するのが、AIを活用した異常検知ソリューション「Impulse」です。
Impulseは機械学習技術を活用して作業工程を分析し、ボトルネックを特定します。まず、現場の作業工程や作業者ごとの時間を計測し、見える化を行います。次に、データを基にボトルネックを分析し、改善策を導入します。例えば、作業工程の最適化や自動化技術の導入、作業者のスキル向上などが含まれます。これにより、サイクルタイムを短縮し、生産効率を向上させることが可能です。