予防保全とは?予防保全の種類と8つの具体例
カテゴリ:活用事例
製造業やインフラ系企業にとって、安定稼働は最重要課題の一つです。しかし、設備の故障は突発的に発生し、多大な損失をもたらす可能性もはらんでいます。そこで注目されているのが「予防保全」という考え方です。
本記事では、従来の事後保全や計画保全とは異なる予防保全の基礎知識を、具体的な種類や事例を交えながら解説していきます。
予防保全とは?
「トラブルが起きてから対応する」のではなく、「トラブルが起きる前に対処する」それが予防保全の基本的な考え方です。
具体的には、設備や機器の状態を常時監視し、異常の兆候があれば、故障に至る前に部品交換や修理などの対応を行う保全方式を指します。生産設備の定期的な清掃や殺菌なども予防保全に含まれます。 これらの活動を通して、設備の寿命を延ばし、製品の安全性を保つなど、様々なメリットが生まれます。
従来の事後保全のように壊れた後に対応するのでは、復旧に時間がかかり、生産活動に大きな影響を与えてしまいます。また、計画保全のように、事前に定めたスケジュールに従って部品交換を行う方法は、まだ使える部品を交換してしまう可能性があり、無駄が生じてしまいます。
予防保全は、これらの課題を解決できる保全方式として注目されている方法です。現在は、 状態監視技術やデータ分析技術の進化により、より精度の高い予防保全が可能になってきています。
予知保全・事後保全・計画保全との違い
設備管理において、適切な保全活動は、設備の長寿命化、生産性向上、そして安全確保に欠かせません。ただ漠然と「壊れたら直せばいい」と考えているだけでは、予期せぬダウンタイムの発生や、高額な修理費用、最悪の場合、重大事故に繋がる可能性も否定できません。
保全活動には、大きく分けて「予防保全」「予知保全」「事後保全」「計画保全」の4つの種類があります。 それぞれのアプローチ方法やメリット・デメリットを理解することで、自社の状況に最適な保全体制を構築することが可能になります。
まずは、4つの保全活動の違いを明確にし、それぞれの概要を掴んでいきましょう。
以下の表は、各保全方法の特徴を比較したものです。
予防保全 | 予知保全 | 事後保全 | 計画保全 | |
定義 | 設備の状態を監視し、異常兆候があれば故障前に対応する保全 | データ分析に基づき、故障発生を予測し、適切なタイミングで対応する保全 | 故障が発生してから修理・交換を行う保全 | あらかじめ定めたスケジュールに基づき、定期的に部品交換や整備を行う保全 |
メリット | ・故障による突発停止を防止 | ・予防保全よりもさらに効率的 | ・対応がシンプル | ・計画的に保全を実施可能 |
・設備の長寿命化 | ・部品交換の最適化によるコスト削減 | ・一時的なコストを抑えられる | ||
・安全性向上 | ||||
デメリット | ・導入コストがかかる場合がある | ・高度なデータ分析技術が必要 | ・故障による損害が大きい | ・無駄な部品交換の可能性 |
・常時監視システムが必要 | ・導入コストが高い | |||
具体例 | ・オイル分析による劣化診断 | ・AIによる故障予測 | ・ランプ切れの交換 | ・法定点検 |
・振動センサによる異常検知 | ・センサデータ分析による残寿命予測 |
予知保全は、予防保全の一種と捉えることもできますが、ここではより高度なデータ分析を用いた保全として区別しています。
予防保全の種類
設備の特性や運用状況に合わせて、最適な予防保全のアプローチを選択することが重要です。予防保全は、あらかじめ定められたタイミングで保全を行う「時間基準保全(TBM)」と、設備の使用状況に応じて保全を行う「利用基準保全(UBM)」に分類できます。
この章では、それぞれの予防保全の種類について、より詳しく解説していきます。
時間基準保全 (TBM)
時間基準保全(TBM:Time-Based Maintenance)は、 定められた時間間隔に基づいて、 定期的に保全活動を実施する手法です。
例えば、
- 設備の稼働時間に関わらず、毎月決められた日に点検を実施する。
- 機械の稼働時間に関わらず、一年ごとにオーバーホールを実施する。
などが挙げられます。
TBMは、 設備の劣化や故障のパターンがある程度予測できる場合に有効な手法です。 計画的に保全を行うことができるため、 設備管理のスケジュールが立てやすく、 保全作業の平準化にも繋がります。
しかし、 実際には設備の劣化状況は個体差や使用環境によって異なり、 必ずしも定められたタイミングで故障が発生するとは限りません。 そのため、 時間間隔が短ければ、まだ使える部品を交換してしまいますし、逆に間隔が長すぎるとトラブルや事故が発生するリスクが高くなってしまいます。
利用基準保全 (UBM)
利用基準保全 (UBM: Usage-Based Maintenance)は、設備の使用状況に基づいて保全活動を実施する手法です。時間基準保全 (TBM)がカレンダーに基づいて保全を行うのに対し、UBM は実際の使用量や負荷を測定し、そのデータに基づいて保全時期を決定します。
一般的には、1日当たりの平均利用量をもとに、メンテナンススパンを算出する方法がとられています。
例えば、
- コピー機の印刷枚数をカウントし、一定数に達したらメンテナンスを実施する。
- 自動車の走行距離を計測し、一定の数値に達したら部品交換を行う。
などが挙げられます。
UBM を導入するメリットは以下の点が挙げられます。
- 設備の実際の使用状況に基づいて保全を行うため、TBM のようにまだ使える部品を交換してしまう無駄を減らすことができます。
- 使用状況を監視することで、設備の劣化状況を把握しやすくなるため、故障の兆候を早期に発見し、突発的な設備停止のリスクを低減できます。
一方で、UBM を導入するにあたっては、以下のような課題も考慮する必要があります。
- 使用状況を正確に測定するためには、適切なセンサやシステムを導入する必要がある場合があり、初期費用がかかります。
- 収集したデータから適切な保全時期を判断するためには、専門的な知識やデータ分析技術が必要となる場合もあります。
UBM は、設備の使用頻度や負荷が大きく変動する環境において、特に有効な保全手法と言えます。
予防保全の具体例8選
ここからは、様々な業界における予防保全の具体例を8つ紹介いたします。 定期的なメンテナンスから、センサやAIを活用した最新事例まで、 自社の課題解決に繋がるヒントがきっと見つかるはずです。
定期的な保全活動
定期的な保全活動は、あらかじめ定められたスケジュールや稼働時間に基づいて、設備の点検、部品交換、清掃などを行う予防保全の基本的な方法です。
この方法は、設備の劣化や故障のパターンがある程度予測できる場合に有効であり、計画的に保全作業を進められるため、管理が容易というメリットがあります。
具体例として、以下のようなものがあります。
自動車業界における塗装ブースのメンテナンス
自動車業界における塗装ブースのメンテナンスは、製品の品質を保つために極めて重要です。塗装ブース内のフィルターを定期的に交換することで、塵や埃の混入を防ぎ、常に高品質な塗装を実現します。
また、塗装ガンの定期的な分解清掃も大切です。塗料の詰まりを防止し、塗装不良や作業遅延を防ぐことで製品の仕上がりが向上し、顧客満足度を高めることができます。
定期的なメンテナンスは、生産効率の向上やコスト削減にも繋がるため、自動車業界において欠かせない取り組みです。
食品業界における定期的な清掃と殺菌
食品を扱う生産設備では、衛生面への配慮が不可欠です。定期的な清掃と殺菌は、設備を清潔に保ち、食中毒のリスクを低減するために重要な予防保全活動です。
製品の安全性が確保されなければ、消費者の信頼を維持することができません。さらに、定期的な清掃と殺菌を行うことで、設備の劣化を防ぎ、生産効率の向上にも寄与します。
食品業界において、衛生管理は品質管理の基礎であり、継続的な取り組みが求められます。
対象の状態に応じた保全活動
前述の通り、定期的な保全活動は、業界を問わず、様々な場面で設備の安定稼働、製品の品質維持、安全性の確保に欠かせません
しかし、定期的な保全活動にも限界があります。
設備の劣化状況は、使用環境や個体差によって異なるため、定期的なメンテナンスだけでは、予期せぬ故障を完全に防ぐことは難しいと言えるでしょう。
そこで、近年注目されているのが、設備や機器の状態を常に監視し、その状態に基づいて保全活動を行う方法です。この方法は、設備の状態をリアルタイムで把握することで、より的確なメンテナンスが可能になるのです。
例えば、以下のようなものがあります。
半導体業界における振動監視
半導体製造装置では、振動の監視も重要な予防保全となります。振動データをリアルタイムで監視し、異常振動が検出された場合にメンテナンスを実施することは、製造プロセスの安定性を保つために有効です。
異常振動は、装置の故障や製品不良の原因となるため、早期に検知し対策を講じることで、ダウンタイムの削減や生産効率の向上を図ることができます。この振動監視システムにより、予知保全が可能となり、計画外のメンテナンスや修理のコストの削減、高品質な半導体製品の安定供給が可能になります。
製薬業界における異音監視
異常音は、機器の異常や部品の摩耗を示すサインです。早期に発見し対処することで大規模なトラブルを回避できます。異音監視システムを導入すれば、機器の状態を常に監視し、必要なメンテナンスを迅速に行うことが可能となります。
製薬業界では、機器から異常音が発生した場合に即座に点検を行い、故障を未然に防ぐ対策が取られています。異音監視システムにより、生産ラインの安定した稼働を維持し、製品の品質を確保できるのです。
故障の予測に応じた保全活動
設備や機器の状態を常に監視し、その状態に基づいて保全活動を行う方法です。
例えば、以下のようなものがあります。
建設業界における使用時間の解析
クレーンやエレベーターなどの大型設備は、建設現場に欠かせません。これらの設備の故障は、作業の遅延や安全性の問題に直結するため、適切なメンテナンスが求められます。従来は、定期的な点検や部品交換が中心でしたが、近年では、センサ技術やデータ分析技術を活用した予知保全の導入が進んでいます。
例えば、クレーンワイヤの外観検査をAIで自動化し、安全性を高めつつ、作業の効率化を図る取り組みが行われています。
予知保全を行えば、故障が発生する前に適切なタイミングで部品交換やメンテナンスを実施することができ、設備の長寿命化と安全性の確保ができるのです。
製造業における機械学習を用いた異常検知
製造業では、生産ラインの安定稼働が求められます。設備の故障は、生産計画の遅延や品質不良、さらには人身事故に繋がる可能性もあるため、未然に防ぐことが重要です。
近年、製造現場では、センサやIoT技術の導入が進み、設備の状態をリアルタイムで監視することが可能になっています。さらに、機械学習を用いることで、収集したデータから異常の兆候を検知し、故障を予測する技術が注目されています。
例えば、生産ラインの製造機器に設置したセンサから、振動、温度、電流などのデータを収集し、機械学習モデルで分析することで、異常な動作パターンを検出することができます。故障が発生する前に適切なタイミングでメンテナンスを実施することができ、設備の長寿命化、生産性の向上、安全性の確保に貢献しています。
このように、予防保全は、製造業や建設業界など様々な分野で、設備の長寿命化、コスト削減、安全性向上に貢献しているのです。
改善のための保全活動
予防保全は、故障の防止や設備の長寿命化に貢献するだけでなく、さらなる性能向上や効率化を図るための活動にもつながります。
ここでは、改善のための保全活動の具体例を紹介します。
電子機器業界における部品のアップグレード
電子機器業界は、技術革新のスピードが速く、新しい部品や技術が常に開発されています。この進化の波に乗り遅れないためには、既存設備への積極的な投資が欠かせません。
例えば、表面実装機(SMT)において、旧式の部品を最新のものにアップグレードすることで、以下のようなメリットがあります。
- 生産効率の向上:
最新の部品は、より高速な処理能力を持つものが多く、アップグレードによって装置全体の処理能力を向上させ、生産性を高めることができます。 - 機能の追加
新しい部品は、従来の部品にはなかった新しい機能が搭載されている場合があり、アップグレードによって装置の機能を拡張できます。 - 省エネルギー化
最新の部品は、省エネルギー設計がされているものが多く、アップグレードによって消費電力を抑え、環境負荷を低減できます。
このように、部品のアップグレードは、設備の長寿命化だけでなく、生産性向上、機能拡張、環境負荷低減など、多岐にわたるメリットをもたらします。
航空業界におけるエンジン部品の改良
航空業界では、安全性を最優先に、エンジンの設計変更による改善が積極的に行われています。より耐久性の高い素材の採用や、構造の見直しによって、エンジンの信頼性を高め、メンテナンス頻度を減らす取り組みが進んでいます。
設計変更によるメリットとしては、以下の点が挙げられます。
- メンテナンスコストの削減
耐久性の高い部品は、交換頻度を減らすことができるため、部品代や作業工数などのメンテナンスコストを削減できます。 - 安全性向上
エンジンの設計変更は、安全性向上にもつながります。耐久性の高い部品や構造は、故障のリスクを低減できるため、航空機の安全運航につながります。
このように、改善のための保全活動は、設備の性能や信頼性を向上させるだけでなく、コスト削減、環境負荷低減、安全性向上など、様々な効果をもたらします。
Impulseによる予防保全の例
「Impulse」は100社、12,000を超える機械学習のモデル運用を支援してきた実績から進化し続けているサービスで、異常検知や要因分析、外観検査など現場の声を反映した機能を取りそろえています。AIと対話しながら機械学習モデルを作成・運用でき、幅広いユーザが業務に機械学習技術を取り入れることができます。Impulseによる予防保全の例を紹介します。
JFEエンジニアリング様における予防保全の導入事例
JFEエンジニアリング様の導入事例では、プラント設備の予防保全のためにブレインズテクノロジーの「Impulse」を導入しました。従来の定期メンテナンスに依存していたため、多大なコストとダウンタイムが発生していました。Impulseの導入により、設備のリアルタイムデータを解析し、異常の予兆を早期に検出することで、計画的かつ効率的なメンテナンスが可能となりました。
ヤンマー様における建設機械の予知保全事例
ヤンマー様の導入事例では、建設機械の稼働状況をリアルタイムで監視し、予知保全を行うために「Impulse」を採用しました。各機械に取り付けられたセンサーから収集されるデータを解析し、異常を早期に発見することで、無駄な点検作業が削減されました。これにより、機械のダウンタイムが短縮され、生産性の向上とメンテナンスコストの削減が実現しました。
ナブテスコ様における産業機器の予防保全実践例
ナブテスコ様の導入事例では、産業機器の故障予防と稼働率向上を目的に、「Impulse」を導入しました。センサーから取得したデータをリアルタイムで解析し、異常を事前に検知することで、突発的な故障を未然に防ぐことができました。、Impulseのデータ解析能力により、より正確なメンテナンス計画が立てられるようになり、機器の寿命延長と生産性向上に大きく貢献しました。
まとめ
この記事では、製造業やインフラ系企業にとって重要な「予防保全」について解説しました。設備トラブルによる損失を抑え、安定稼働を実現するために、予防保全は欠かせない考え方です。
従来の事後保全や計画保全とは異なり、予防保全は設備の状態監視やデータ分析を駆使し、故障の兆候をいち早く捉え、適切なタイミングでメンテナンスを実施します。
定期的なメンテナンスはもちろんのこと、センサやAIを活用した状態監視技術を用いることで、より精度の高い予防保全が可能となります。
これらの事例から、予防保全が設備の長寿命化、生産性向上、安全性向上に貢献することがご理解いただけたと思います。
次のステップとして、自社の設備や現状の課題を踏まえ、最適な予防保全のアプローチを検討してみてはいかがでしょうか。
関連記事:AIを活用した予兆検知とは?検知の手法とAI活用のメリットをご紹介
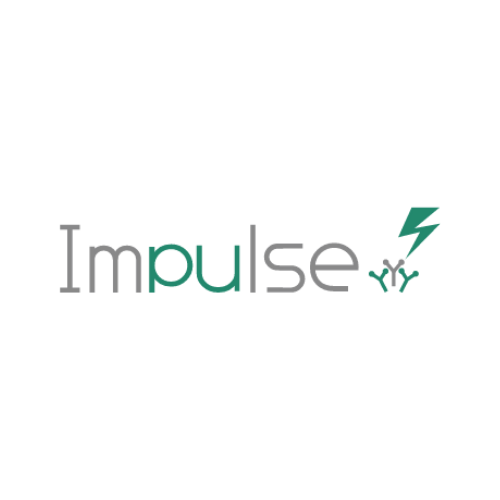
- Impulseによる予防保全
- Impulseは機械・設備の停止や故障に繋がる予兆を、最新のAIによって捉える分析アプリケーションです。機械学習技術の実用化を目的に、2014年市場に先駆けてリリースされ、数多くのお客様の”現場で鍛え上げられた”異常検知ソリューションです。
企業活動にかかわる、複雑で膨大なセンサーや音声や画像などのデータを収集・可視化する基本機能に加え、従来の閾値ベースの管理では発見できない障害や故障予兆の検知要因の追究など、これまで対応困難であった業務課題に対し、機械学習を武器に新たなアプローチで現実解を導きます。