チョコ停を引き起こす6つの原因とそれぞれへの対策
カテゴリ:基礎知識
チョコ停は一見小さな問題に見えるかもしれませんが、累積すると生産性に大きな影響を与える問題です。
今回は、チョコ停の原因を6つの項目に分類し、それぞれの原因と対策を解説していきます。
目次
チョコ停とは
チョコ停は、製造ラインにおいて短時間かつ頻繁に発生する小規模な停止のことを指し、JISでは以下のように規定されています。
設備が生産ラインなどの大規模なシステムの一部となっていて、システム全体を停止に至らしめるような重大または決定的な故障を大故障(通称としてドカ停、逆に設備の部分的な停止または設備の作用対象の不具合による停止で、短時間に回復できる故障を小故障(通称としてチョコ停)という。
具体的な停止時間は決められていないため、業界や企業によってチョコ停の定義は異なるかもしれません。
これらの短時間の停止は個々では大きな問題に見えないかもしれませんが、累積すると生産性に大きな影響を与える可能性があります。
ここで、設備稼働率(機械稼働率)は以下の式で表されます。
稼働可能な総時間が12時間の設備を考えてみましょう。
【チョコ停を含まない場合】
1日あたり以下の条件で設備が稼働したとします。
- 稼働可能な総時間:12時間
- 実際の稼働時間:9時間(うちチョコ停は1時間)
チョコ停を含まず設備稼働率を算出すると
(9時間÷12時間)×100=75%
となります。
【チョコ停を含めた稼働率】
上記と同様の条件で設備が稼働しており、チョコ停を含めて設備稼働率を算出すると
{9時間÷(12時間+1時間)}×100=69%
チョコ停を含めたときと含めないときの稼働率の差が、チョコ停による稼働率低下を示します。
今回の例では、チョコ停により、6%稼働率が低下したことになります。
チョコ停止の原因の分類とそれぞれへの対策
製造ラインにおけるチョコ停の原因は多岐にわたりますが、効果的な対策を講じるためには、これらの原因を体系的に分類し、理解することが重要です。一般的に、チョコ停の原因は以下の6つの主要な項目に分類することができます。
- 部品や材料
- 部品の固定
- 加工や作業を行う部分
- 動力を伝える部分
- モーターやエンジン
- センサーや制御システム
各項目に特化した対策を講じることで、チョコ停の発生を効果的に減少させ、生産性を向上させることができます。
ここからは、これら6つの項目それぞれについて、具体的な原因と対策を詳しく説明していきます。
部品や材料
部品や材料に問題があると、製造工程全体に影響を及ぼし、チョコ停の主な原因となります。ここでは、部品や材料に関するチョコ停の原因とその対策について詳しく解説します。
原因
部品や材料に関する問題は、チョコ停の主要な原因の一つです。具体的には、以下の2つが原因として挙げられます。
【部品や材料の品質不良】
製造ラインに投入される部品や材料の品質が不十分な場合、製造プロセスの途中で問題が発生し、ラインの停止につながる可能性があります。
例えば、部品の強度不足、表面仕上げの不良、材料の不純物混入などです。これらの品質不良は、製造工程での不具合や製品の品質低下を引き起こし、結果としてラインのチョコ停が発生してしまいます。
【サイズや形状の不適合】
部品や材料のサイズや形状が規格に合っていない場合も、チョコ停の原因となります。例えば、部品が大きすぎて取付け箇所にフィットしない、あるいは小さすぎて適切に固定できないなどの問題です。
形状の不適合は、組み立て工程でのミスや機械との干渉を引き起こし、ラインの停止につながる可能性があります。
これらの問題は、製造ラインの効率を直接的に低下させるだけでなく、製品品質の低下や後工程での問題の発生など、二次的な影響も大きいため、早急な対策が必要です。
対策
部品や材料に関する問題に対処するためには、品質管理の強化が不可欠です。ここでは、効果的な対策を詳しく説明します。
品質管理の強化
部品や材料の品質不良やサイズ・形状の不適合によるチョコ停を防ぐためには、以下の対策が有効です。
【受入検査の徹底】
サプライヤーから納入される部品や材料の品質を確保するため、受入検査を徹底します。具体的には以下の方法があります。
- サンプリング検査の頻度を上げる
- 全数検査の導入(特に重要な部品や材料に対して)
- 自動検査システムの導入(寸法測定、外観検査など)
- 検査員のトレーニングと定期的なスキルチェック
【品質基準の明確化】
部品や材料の品質基準を明確に定義し、サプライヤーと共有することも重要です。
- 詳細な品質仕様書の作成と定期的な見直し
- サプライヤーとの品質会議の定期開催
- 品質データの共有と分析
- 不適合品に対する是正措置プロセスの確立
これらの対策を実施することで、部品や材料に起因するチョコ停を減少させることが可能です。また、品質管理の強化は製品の品質向上にもつながるため、顧客満足度の向上や返品・クレームの減少といった副次的な効果も期待できます。
部品の固定や保持
部品の位置ずれや脱落、機械の精度低下などが発生すると、チョコ停の原因となります。ここでは、部品の固定や保持に関するチョコ停の主な原因と、それに対する効果的な対策について詳しく解説します。
原因
部品の固定や保持に関する問題は、主な原因として以下の2つが考えられます。
【位置決めの誤差】
位置決めの誤差は、部品や製品が正確に所定の位置に配置されない状況を指します。この問題は以下のようなことが原因で発生する可能性があります。
- 位置決め機構の精度不足
- 機械の振動や摩耗による位置ずれ
- センサーや制御システムの誤作動
- 作業者の操作ミス(手動位置決めの場合)
【保持部の摩耗や損傷】
保持部とは、部品や製品を固定するためのクランプ、チャック、治具などの機構を指します。これらの保持部に摩耗や損傷が生じると、以下のような問題が発生する可能性があります。
- 部品の固定力低下による脱落や位置ずれ
- 保持部の変形による部品との不適合
- 摩耗による精度低下
- 損傷による突発的な故障
保持部の摩耗や損傷は、長期間の使用や過負荷、不適切なメンテナンスなどが原因で発生します。保持部が摩耗したり破損したりすると、部品の固定不良や加工精度の低下を引き起こし、チョコ停の原因となります。
対策
部品の固定や保持に関する問題に対処するためには、以下の対策が効果的です。
【クランプや治具の定期点検と交換】
クランプや治具も破損する可能性があることを考慮し、以下のような対策を実施しましょう。
- 点検スケジュールの確立と定期的な点検の実施
- 適切な交換基準の設定
- 予備品の確保
- 定期的なメンテナンスの実施
【位置決め装置の精度確認】
位置決め装置の精度は、製品品質と生産効率に直接影響を与えます。精度を維持するために、以下の対策を行いましょう。
- 定期的な精度測定
- 校正プログラムの実施
- 湿度や温度、振動対策など環境管理
- オペレーターのトレーニング
定期的な点検や精度確認は、突発的な故障を予防するために欠かせない項目です。
加工や作業を行う部分
製造ラインの心臓部とも言える加工や作業を行う部分は、製品の品質と生産効率を直接左右する重要な工程です。この工程でトラブルが起これば、製品の製作に大きな影響を与えかねません。ここでは、加工や作業部分に関連するチョコ停の主な原因と対策を解説します。
原因
加工や作業工程のトラブルは、直接的にチョコ停を引き起こす可能性が高く、その原因は主に以下の3つがあります。
【刃物や工具の摩耗】
刃物や工具の摩耗は、加工精度の低下や不良品の発生につながります。例えば以下のようなことが考えられます。
- 切削工具の刃先が摩耗したことによる、切削性能の低下
- 金型の摩耗による成形不良
- 溶接電極の劣化による溶接品質の低下
【作業者の設定ミス】
作業者の設定ミスは、以下のような問題を引き起こします。
- 加工位置のずれによる不良品の発生
- 工具の取付け角度の誤りによる加工不良
- ロボットアームの動作範囲の誤設定による干渉や衝突
【加工速度や圧力の不適合】
加工速度や圧力が適切でない場合、以下のような問題が発生します。
- 加工速度が速すぎることによる加工不良や工具の早期摩耗
- 圧力が強すぎることによる部品の変形や破損
- 速度や圧力が不足することによる加工精度の低下や接合不良
例えば工具の摩耗が進むと適切な加工速度や圧力も変化するため、総合的な対策が必要です。
対策
加工や作業工程でのチョコ停を防ぐためには、根本的な原因を理解し、効果的な対策を講じることが大切です。以下に示す対策でチョコ停の撲滅を目指しましょう。
工具の管理
工具の管理は、加工精度と生産効率を維持するための基盤です。安定した加工を実現するためには、以下の対策が効果的です。
【工具の使用時間管理と交換スケジュールの確立】
工具の摩耗を予測し、適切なタイミングでの交換を行うために、以下のような対策を実施しましょう。
- 使用時間の記録
- 交換スケジュールの設定
- 点検の実施
【高品質な工具の使用】
耐久性が高く、精度の良い高品質な工具を選定することで、加工時のトラブルを減少させます。以下の点に注意して工具を選定、使用しましょう。
- 工具選定基準の設定(高品質な工具の使用)
- 信頼性の高い供給元の確保
- 導入時のテストと検証の実施
各メーカーの特性や工具自体の特徴をふまえた上で、自社の工程に適した工具であるか検証しましょう。工具は消耗品ですから、定期的に点検と交換を行うことを忘れてはいけません。
作業手順の標準化
作業手順が標準化されていれば、作業の一貫性を保ち、人為的ミスを最小限に抑えることができます。作業手順の標準化のポイントは以下のとおりです。
- 詳細かつ分かりやすい記述
- チェックリストの導入
- 安全注意事項の明記
- 作業手順の定期的な見直し
- 最新技術の反映
作成した作業手順の資料は、タブレットやデジタルディスプレイ等を活用し閲覧できるようにすれば、最新の情報をいち早く共有できます。
動力を伝える部分
動力伝達システムは、機械の心臓部とも言える部分です。ここでは、動力伝達システムに関連するチョコ停の主な原因と、それらを防ぐための対策について解説します。
原因
動力を伝える部分は、機械の動力源から実際に作業を行う部分へエネルギーを伝達する役割を果たします。このエネルギーはベルトやチェーンによって伝えられているため、これらのトラブルは、製造ラインの停止に直結します。以下の症状には注意しましょう。
- ベルトの緩みや破損
- チェーンの摩耗
- チェーンの伸び
- チェーンの破断
適切な保守点検や予防的メンテナンスにより、動力伝達部分の破損リスクを大幅に軽減することができます。
対策
動力伝達システムのチョコ停を防ぐためには、定期点検と予防保全が欠かせません。以下の対策を実施することで、動力伝達システムの安定性を高めることができます。
定期点検とメンテナンス
【ベルトやチェーンの定期的な点検と交換】
ベルトやチェーンに緩み、摩耗、破損がないか定期的に点検しましょう。必要に応じて潤滑剤も追加します。以下の2点を行っておくことで、点検作業がスムーズに行えます。
- 交換基準の設定
- 点検記録の作成
【ギアの噛み合わせ調整】
噛み合わせのズレは、動力伝達の効率を低下させ、異常摩耗や故障の原因となります。以下の点に注意し調整を行います。
- ギアの歯の接触状態
- 異常な摩耗や破損の有無
- ギアのバックラッシュ(隙間)の状態
予防保全の導入
予防保全を導入すれば、動力伝達システムのトラブルを未然に防ぎ、長期的な稼働ができるようになります。以下の対策を実施しましょう。
【定期メンテナンススケジュールの作成】
動力伝達システムの各部品に対して、定期的なメンテナンススケジュールを作成し、計画的な点検と保守を行います。スケジュールには、点検項目、頻度、交換時期などを明確に記載し、確実に実施しましょう。
【振動や異音の早期検出システムの導入】
動力伝達システムにおける異常を早期に検出するためのシステムを導入します。振動や異音をモニタリングし、異常が発生した際にアラートを発することで、早期対応が可能になります。
モーターやエンジン
モーターやエンジンは製造ラインの動力源として不可欠な存在です。これらの重要機器に問題が生じると、予期せぬラインの停止や生産性の低下を引き起こします。ここでは、モーターやエンジンに関連するチョコ停の主な原因と対策について詳しく解説します。
原因
モーターやエンジンは製造ラインの動力源として重要な役割を果たしますが、これらに問題が生じるとチョコ停を引き起こす可能性があります。主な原因として以下の3点が挙げられます。
【モーターの故障】
モーターの故障は、以下のような原因で発生します。
- ベアリングの摩耗や損傷
- 巻線の絶縁劣化や断線
- 過負荷による焼損
- 冷却不足による過熱
【駆動部のオーバーヒート】
駆動部のオーバーヒートは、以下のような原因で発生します。
- 冷却システムの不具合や能力不足
- 潤滑油の不足や劣化
- 過負荷運転
- 環境温度の上昇
【エネルギー供給の不具合】
エネルギー供給の不具合には、以下のようなものがあります。
- 電源の不安定性(電圧変動、瞬間停電など)
- 配線や接続部の劣化
- 燃料供給システムの問題(エンジンの場合)
- 電力変換装置の故障
対策
モーターやエンジンに関連するチョコ停を防ぐためには、温度管理と冷却システム、定期的な点検、予防保全の導入が不可欠です。ここでは、それぞれの対策を詳しく説明します。
温度管理と冷却システム
モーターやエンジンのオーバーヒートを防ぐためには、適切な温度管理と冷却システムが必要です。以下の対策を講じることで、駆動部の過熱を防止し、安定した稼働を維持することができます。
【駆動部の温度管理システムの導入】
駆動部の温度をリアルタイムで監視し、異常が発生した場合に即座に対応するためのシステムを導入します。
【適切な冷却システムの設置】
モーターやエンジンを適切に冷却するために、効率的な冷却システムを設置します。
定期的な点検
モーターやエンジンの定期的な点検とメンテナンスは、チョコ停を防ぐための重要な対策です。以下のポイントを押さえた上で定期的にメンテナンスを実施し、設備の安定稼働を実現させましょう。
- 点検スケジュールの確立
- 重点的な点検項目の設定
- 予防保全の実施
- データ管理とトレンド分析
- 専門技術者の育成
- 外部専門家の活用
センサーや制御システム
製造ラインの自動化と効率化の要となるセンサーや制御システムは、その精度と信頼性が生産性に直結します。ここでは、センサーや制御システムに関連するチョコ停の主な原因と、それらを防ぐための対策について解説します。
原因
センサーや制御システムは、製造ラインの自動化と効率化に不可欠な要素ですが、これらに問題が生じるとチョコ停の原因となります。主な原因として以下の3点が挙げられます。
【センサーの誤動作や故障】
以下のような場合、センサーの誤動作や故障が発生する可能性があります。
- 経年劣化や環境ストレスによる故障
- 汚れや異物の付着による誤検出
- 電磁ノイズによる誤作動
- 設置位置のずれや振動による誤検知
【制御システムの設定ミス】
以下のような制御システムの設定ミスは、製造プロセス全体に影響を与える可能性があります。
- パラメータの不適切な設定
- 制御ロジックの誤り
- タイミング設定の不適合
- 異常時の対応設定の不備
【ソフトウェアのバグやエラー】
以下のようなソフトウェアの問題も、チョコ停の原因となります。
- プログラミングエラー
- システムの互換性の問題
- アップデート後の不具合
対策
前述の通り、センサーや制御システムは様々な原因で問題が発生してしまいます。製造ラインの安定稼働を維持するためには、以下のような対策が必要不可欠です。
センサーとシステムの定期点検
センサーは製造ラインの各種データを正確に取得するための重要な役割を果たしています。定期的な校正や点検を実施することで、センサーの精度を維持し、誤作動を防ぎます。定期点検を実施する場合は、以下のポイントを押さえておきましょう。
- 校正や点検のスケジュール確立
- データの記録
トレーニングと教育
製造ラインのセンサーや制御システムの効果的な運用には、オペレーターや技術者の適切なトレーニングと教育が欠かせません。ここでは、オペレーターや技術者が押さえておくべきポイントを説明します。
【オペレーターと技術者の定期的なトレーニング】
具体的には以下のようなトレーニングが推奨されています。
- 基本操作の再確認
- トラブルシューティング演習
- 最新技術の習得
- クロストレーニング(部門横断的なトレーニング)
【新しいシステムやソフトウェアの導入時の教育】
以下のようなステップを踏んで、段階的に新しいシステムやソフトウェアを導入しましょう。
- 段階的な導入トレーニング
- ハンズオントレーニング
- マニュアルとガイドラインの整備
- フォローアップセミナー
- 学習環境や問い合わせ先の提供
まとめ
チョコ停は製造ラインの効率を大きく低下させる要因であり、その対策は製造業にとって重要な課題です。本記事では、チョコ停の主な原因を6つの項目に分類し、それぞれに対する具体的な対策を提示しました。
それぞれの項目ごとの特徴はあるものの、総じてメンテナンスや検査が大きな役割をはたしていることがわかります。
製造業において、チョコ停対策は継続的な改善活動の一環です。常に最新の技術や方法を取り入れながら、生産性と品質の向上に努めましょう。
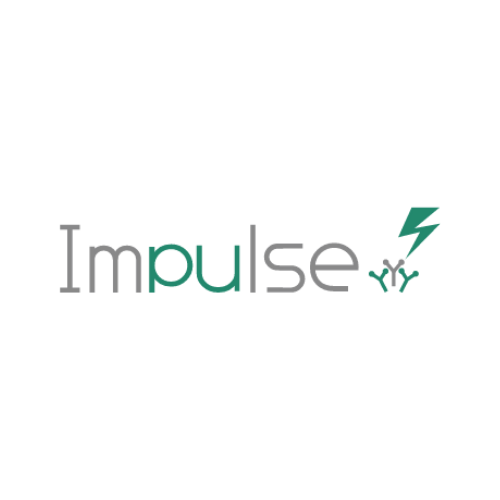
- Impulseによるチョコ停対策
- Impulseは機械学習技術の実用化を目的に、2014年市場に先駆けてリリースされ、数多くのお客様の「現場で鍛え上げられた」異常検知ソリューションです。企業活動にかかわる、複雑で膨大なセンサーや音声や画像、動画などのデータを収集・可視化する基本機能に加え、従来の閾値ベースの管理では発見できない障害や故障予兆の検知、不良品の検出、作業工程の確認・分析、要因の追究など、これまで対応困難であった業務課題に対し、機械学習を武器に新たなアプローチで現実解を導きます。
機械学習を活用した高度なデータ分析処理に加え、業務に組み込んだシステムとして導入・運用するために必要な様々な機能を統合的に備えたプラットフォームであるため、チョコ停防止にも貢献できます。